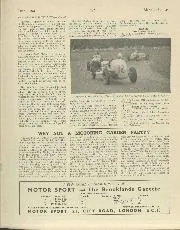
WHY NOT A MOTORING GARDEN PARTY?
WHY NOT A MOTORING GARDEN PARTY? On May 9th, at Heath Row Aerodrome, the Royal Aeronautical Society held their annual :Garden Party, attended by almost everyone who is anyone in…
HAVING equipped the workshop with a bench, vice, and a few other necessaries of life, there is time to look round awhile, before launching forth into erratic expenditure on devices which may or may not assist in the better running and repair of the automobile for whose benefit the whole trouble is being taken. Cars themselves vary so much in their accessibility, to say nothing of their need for repairs, that it will depend greatly on the make which is favoured, what equipment will be necessary when working on it.
Every year shows some improvement in this respect, and it is no longer so common to find cars on which the back axle has to be detached before the engine can be taken out, or on which the gear box has to be dismantled to remove the sump !
Therefore, the best thing to do is to tackle a few dismantling jobs with the equipment already mentioned and get an idea thereby what sort of additions will have to be made to avoid excessive wear and tear on the vocal chords.
Start Right.
Most amateur tuners begin entirely at the wrong end when trying to make their cars better and brighter, and are apt to think that the engine is the only thing that requires tuning ; and even then they usually start where they ought to finish. I do not propose at the moment to go into a long harangue on raised compressions, polished ports, etc., but to suggest ways and means for keeping the vehicle in such a condition that it will maintain its original performance with some degree of safety and reliability. This being so, we can consider the ordinary routine repairs, and leave the problems of ” hotting-up ” till later.
It is remarkable how many owners are perfectly content to work hard on an engine and continue to drive it about the country in a chassis which gets more and more unsafe with everg mile covered. This is the second of a series of articles dealing with the equipment, use and maintenance of the
workshop at home.
Therefore, get in the habit of keeping the chassis up to the mark before bothering about the engine.
Sooner or later the brakes will want relining, but this is the least attention they will need. Modern brake linings have such wonderful wearing properties that they are apt to encourage neglect of the braking system in general. Modern cars have wonderful brakes, provided always that there is a reasonable means of applying them. There are, unfortunately, many things to happen between the pedal and the shoes, in the way of cross shafts, etc., which may be partially seized up, and so give the impression that the brake linings have nearly given up work. Actually, in many cars, most of the pedal pressure is used in overcoming such intermediate resistances, and unless the mechanism is well looked after, the best linings in the world will be useless. However, when the brakes actually do need relining, there is nothing unduly complicated in the job, as it merely consists of removing the drums, taking off the shoes, fitting the new linings and reassembling. You can always see that on a garage bill for the job, and put like that, it seems too easy! All the same, those simple words may cover much bad language. and a consideration of the more obvious snags may show that the money charged on the said bill has been well earned. Removing the brake drums is the first trouble as a rule, for the simple reason that they must not be liable to
come off when running, and are therefore put on to stay put.
In cases where the drums bolt on to the hubs, the job is fairly straightforward, and although requiring considerable strength, needs no special equipment. When the drum and hub are one, and held on to a tapered shaft, it may not be possible to remove them without special weapons, but an attempt can at least be made. Having got the axle firmly supported on d box or block (jacks are too liable to get pushed over to be safe), the hub exposed and the nut on the shaft removed, everything is ready to be removed.
The first method is to get a couple of levers behind the drum and apply gentle pressure, at the same time tapping the end of the shaft with the heaviest hammer available. A piece of lead should be held against the end of the shaft while tapping to avoid damage to the thread.
Removing Shafts.
In any ease of hitting shafts to drive them through anything, the heaviest hammer should be used that is consistent with getting at the job easily. A small hammer used hard tends to have only a local effect. That is, it tends to spread the end of the shaft instead of moving the whole shaft. A comparatively gentle blow with a heavy hammer will have far more effect, while a really hard hit with a very heavy hammer, although effective enough, requires considerably more skill than at first seems obvious, if nothing is to be damaged. In fact, it might be said. that the ability to employ extreme violence without causing any damage, is one of the hall-marks of a good mechanic. The reason for the respective uses of large and small hammers will be obvious to anyone acquainted with the mechanics of momentum and impacts, but these do not much matter so long as the effects are remembered. Some hubs leave their tapers more easily than others, depending chiefly on
the angles of the tapers, and on how tightly they were originally fitted to them. If the preliminary skirmish described above fails to get the hub off, it is no use trying a more violent variation of the same treatment, hitting the drum itself. Either of these courses will merely cause damage, probably in the shape of an untrue brake drum. An increasing number of manufacturers are now including a wheel drawer in the tool kit, but if your model is not so blessed, one can usually be obtained from the works, at a price. It may here be mentioned that the price of this tool appears to bear no relation whatever to the cost of making it, and it may cost anything from three or four shillings to well over a pound, for the simple screw-on variety to suit one hub size only. •
The screw-on type are far the most efficient, and should always be used in preference to those with jaws designed to hook over the part to be withdrawn. These are adjustable, it is true, and for some repair work in a service station, also for pulling sprockets and similar rigid objects, are very useful, but for car hubs are practically useless. If the jaws are used on the drum itself, usually the only possible way, the drum, unless very heavy, will suffer.
If the makers do not supply a drawer, or the owner does not feel like paying for one, it can usually be improvised with a little trouble. If the car has wire wheels with screw-on hub caps, a good wheelpuller can be made from a spare cap. The normal screw-on puller consists of two parts : the outer casing which screws on in place of the hub cap, or on a thread on the hub specially provided, and a bolt which screws through the centre of this and presses against the end of the shaft. The hub cap provides the basis of one half, while a large bolt for the other part can be purchased quite cheaply. It is worth getting a special bolt of high tensile steel, as a soft bolt may easily bend under the stress. I have seen various home-made hub drawers of this type, and the usual failing has been the insufficient thickness of the cap, with the result that when it is drilled and tapped, the thread is not deep enough, and To drill and tap it alone is
not enough. It should be7drilled, and a nut of the correct size brazed in position in the centre of the cap, on the inside. If about a I” bolt is used, this should make up a tool which will do as well as the works variety. If the works job costs only five or six shillings, it is not worth making up unless the owner can do the complete job himself, but if the cost is much more than this, it will be a good saving, even if the job has to be done outside.
If the wheel is held by three or five studs, and the wheel is on its own hub cap, as is the case with many wire wheels to-day, not much can be done in the way of improvisation, but if it is an artillery wheel with a cover also held on by the studs, a puller can be made in the same way as before, only substituting the cover for the hub cap. If the cover is only thin sheet, this will, of course, be no use, but some makes are quite strong enough to be used as suggested.
With modern cars, splined shafts are being used extensively for securing hubs, and in this case there is never likely to be the grim struggle which sometimes occurs when a hub and its taper take a particular fancy to each other. Hubdrawers may still be required, but are not so likely to be over-strained. Hubs are far from being the only things which have to be pulled off their shafts, and many cases may arise where there appears to be absolutely nothing short of dynamite which will move things. As the control of dynamite is somewhat difficult, we must turn to more prosaic methods, and I have often wondered why so many people fail to realise that in the humble jack provided with the car there is a weapon of immense power with many
uses other than lifting the vehicle ; that is, providing the jack is a good one, and not one of the wretched affairs which sometimes appear in the tool kits of cars which one comes across occasionally. Recently I was confronted with a back axle which required a new crown-wheel. Having duly removed it from the car and removed the hubs (a puller was available) I started to dismantle it. It was of the split casing type in which each half slides off over the shafts after the bolts are
removed from the joint. At least that is the general idea, but in this particular case the bearings at the outer end of each. road shaft had become as one with the shaft itself. The car’s wheel drawer had done its work, but it could only tackle one job, and this was not it. Obviously a special weapon was required, as this particular piece of stickiness is, fortunately, a fairly rare occurrence.
A Satisfactory Makeshift.
After a certain amount of attention with such weapons as lay to hand, a device was constructed. This consisted of heavy straps embracing substantial portions of the end of the axle casing with one end, and supporting the base of a jack with the other, what time the top of the jack pressed against the end of the axle shaft. The straps consisted of four hall-inch steel rods threaded and fitted with two nuts. each end, and passing through cross pieces of very heavy angle iron. One pair of these supported the base of the jack, while the other pair went behind suitable bosses on the axle casing. Naturally, in a makeshift job of this kind a certain. amount of wangling is required, but by suitable adjustment of the nuts the improvised wheel drawer was squared up. and pressure applied in the usual manner, but with considerably increased power. The mistake was made at first of using a simple, light jack, and the very high pressure reached merely burst the base of it. The ball races in question were secured to the shafts with the rust of ages, a state of affairs which should not occur on a properly maintained vehicle. The substitution of a heavy double-lift jack for the first effort, and the use of a turning bar 3 feet long in place of the usual handle, produced the desired result.
The pressure exerted may be imagined from the fact that a jack which will lift half a ton with a turn of the wrist required a man’s full strength on the lever used tomove the shaft. The above is rather a digression from the subject of relining_ brakes, but is given as an example of the cheap and homely methods which may be applied to refractory fly-wheels and other parts, in the absence of more specialised tools. No one would maintain that the treatment is likely to do the jack any particular good, but in the case of a screw type jack it will not do it any harm, if a certain amount of discretion is. used.
Once the brake shoes are exposed, by fair means or foul, and cleaned, the actual relining is simple enough. The old rivets can be cut and punched out of the shoes quite easily, and the new linings applied. Obviously the one real essential is to. make the lining lie absolutely flat on the ‘shoes, as if it tends to ” hump ” between the rivets it will be impossible to get good braking. If you can get ready cut and drilled linings, and Ferodo now make up sets of die-pressed linings for nearly every make of car, it is almost impossible to go. wrong. If, however, the lining is not drilled, a little more care may be needed. Start at one end of the shoe and drill and.
countersink the holes, and then rivet this end before drilling any further holes. The next set of holes along the lining can then be drilled, using the holes in the shoe as a guide. If the drill is used at a slight angle it will ensure the lining being stretched tight. By drilling and rivetting round the shoe there will be no errors due to attempting to mark and drill all the holes in the lining before fitting.
Final Touches.
In the actual rivetting some suitable support for the rivet head is needed, and a punch or small chisel, held in the vice with the handle upwards, will be found convenient for supporting the head of the rivet, while the lower end is spread over with a light hammer. When the lining is fitted, the ends should be bevelled off with a file to about half the original thickness. This ensures a good lead for the braking surface and makes for smoother and more even braking. In the operations outlined in this article some items of equipment not included in the simple tools mentioned in the first article of this series will be required. A bench drill was included in these, but a hand or breast drill (quite a light, cheap one, will do) must be added for such jobs as drilling the brake linings. The manufacture of improvised wheel drawers will
other jobs in connection with a motor car, to say nothing of truing up threads damaged in dismantling,a good set is worth getting, at least in sizes up to 4-inch. Most cars employ both 13.S.F. and Whitworth threads, but some manufacturers are coming down to B.S.F. as standard. This, being a finer thread, is stronger and less liable to vibrate loose.
With careful usage, and a sharp eye on friends who wish to borrow them, these items will last almost indefinitely, while if the cost of a complete set appears too much, they can be acquired singly. This method is more expensive, however, and the danger of losing parts, much greater than if they are in a case.
To keep drills O.K.
Another item which is necessary to keep drills in condition is a grinding wheel. A hand grinder, of good ntake, will suffice, but the convenience of a small electric grinder is very great. A small polishing motor of about k h.p. with a suitable emery wheel mounted on the shaft, makes an excellent instrument, and the first cost will never be regretted. It can be used for scores of different jobs.
W. S. B.