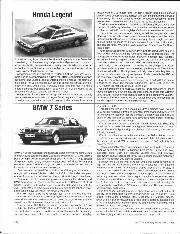
New Cars: Honda Legend
It is astonishing how different the Honda Legend is to the Rover 800 considering they have so many components and panels in common and, indeed, are built in the same…
common supposition that an engine could not be expected to work at its maximum power until a long time after the cylinders had been bored and new pistons fitted. Happily, this objection has now become nonexistent and the type of machine illustrated on page 312 is capable of giving marvellously accurate results, even in cases where straight-eight cylinder blocks have to be reground in one setting.
The work is mounted firmly on a large table provided with a cross traverse, which can be adjusted accurately in relation to the distances between the centres of the cylinder bores and is described as being of the ” generative ” class, that is to say, the grinding wheel has imparted to it a planetary motion whilst rotating at high speed on its own axis, the planetary spindle being eccentrically adjustable whilst the grinding process is in operation. This particular machine, which is installed at the Laystall Works, is one of the very few of its capacity in this country and represents the very latest practice in this class of machine tool. It is of interest to note that with this machine the speed of the grinding wheel is from between 5,500 and 6,50o feet per minute and the finish of the bore surfaces is greatly influenced by the careful selection and grading of the wheels, which is one of the closely guarded secrets of the specialist on this class of work.
Even with modern machinery of this class, a very great amount of care is required to keep it in the necessary condition for maintaining the accuracy of the work and nothing can be left to chance in keeping it in firstclass order.
Reducing Compression Space.
The ease with which compression space can be reduced by decreasing the thickness of cylinder gaskets sometimes gives rise to the erroneous impression that the work of the machinist in making further reductions is equally simple. On the contrary, however, the operation of machining down the surfaces of cylinder bases and cylinder heads calls for the use of somewhat elaborate machinery, and as the process of grinding is generally recognised as being more accurate than shaping
or surface milling, we have to employ the type of vertical surface grinding machine, the general lay-out and proportions of which can be gathered from the photograph reproduced beow. In this case the work is mounted on a traversing table, which moves backwards and forwards with an automatic reversing feed, allowing the surface to be ground to come into contact with the abrasive wheel, which has a speed of about 4,000 feet per minute and consumes about Do horse-power, so that grinding of this type is not exactly a very cheap operation. The advantages of finishing off a surface with the smoothness only obtainable by surface grinding are obvious, when the normal difficulties of securing a perfect fit for the cylinder head gaskets are realised, and furthermore, the work can be done with far greater speed than is possible when the material is removed by cutting tools, as distinct from abrasive wheels.
Making Oversize Pistons.
Whilst the question of compression is under discussion, I suppose I am expected to say something about the aluminium alloy v. lightweight cast iron forms of piston, but this is too intricate a matter to enter upon in the space available. Racing motorists are generally in favour of the former and no doubt they are the best judges, but at the same time, it is surprising to find how many competition drivers elect to use pistons of cast iron by virtue of certain advantages which the latter possess, whilst we are continually called upon to supply cast iron pistons to replace those of the aluminium type as fitted to certain makes of cars. In making special oversize pistons for engines where a higher compression ratio is required, it is a simple matter to effect a slight alteration in the position of the gudgeon pin hole, thus bringing the crown of the piston nearer to the top of the combustion chamber, with a resulting decrease of compression space. With highly finished surfaces for both the cylinder bores and the new pistons, it is possible to work to closer limit than when the respective surfaces are left less smooth